SkySport Tech - In una monoposto di F1 ogni elemento ha una valenza prestazionale, ed uno fondamentale oltre che per la principale funzione per cui è stato progettato è l’impianto frenante. Eccone tutti i segreti su una pista molto esigente come quella di Montreal
Quando parliamo di efficienza, ovviamene ci riferiamo alla capacità che l’impianto frenante ha di far decelerare rapidamente la vettura, nel minore spazio possibile. Questo, è di fatto lapalissiano, quasi un ABC, per neofiti della materia. Il sistema frenante di una F1 è infatti un sistema complesso di elementi, che contribuiscono non solo alla frenata ma, da quando sono state introdotte le Power Unit ibride, anche al recupero di parte dell’energia, altrimenti dissipata nella fase di decelerazione. Effettuare un viaggio tra tutte le sue componenti e capirne il funzionamento, può essere un’esperienza affascinante.
Un sistema complesso
Incominciamo con separare la pura descrizione dei singoli elementi (meccanici e con funzione aerodinamica di ventilazione) dal complesso funzionamento del sistema, che include per quanto riguarda i freni posteriori l’azione del sistema Brake by Wire, collegato alla MGU-K per il recupero dell’energia cinetica. Come noto, e visibile ogni volta che una monoposto è ferma ai box priva delle ruote, i freni, o meglio, i dischi e le pinze sono carenate da cestelli in fibra di carbonio, che sono parte integrante sia delle prese d’aria di raffreddamento, sia del sistema di ventilazione stessa dei dischi, e di trasmissione del calore alle gomme attraverso i cerchioni. Sono infatti ben visibili sia di fori, talvolta con profilo a goccia, per la trasmissione del calore generato in frenata ai cerchi, sia di raffreddamento del disco. Spesso nella parte superiore del cestello sono realizzate delle feritoie di maggiori dimensioni, di sezione rettangolare, poste proprio in corrispondenza del disco celato all’interno del cestello. Queste hanno la primaria funzione di smaltimento del calore nelle condizioni che di solito si incontrano sui tracciati cittadini, cioè quando mancano rettilinei significativi, implicando un innalzamento oltre i limiti della temperatura del disco.
La gestione delle temperature
Se apriamo un cestello, ad esempio uno posteriore, possiamo identificare i vari componenti. Il cestello stesso che è spesso caratterizzato da nervature esterne per facilitare l’estrazione dell’aria attraverso le razze del cerchione, deviando all’esterno le turbolenze generate. All’interno notiamo coricata inferiormente, per mantenere un centro di massa il più basso possibile, la pinza che ha un peso complessivo di circa 1.3 kg massimo a seconda delle tipologie. E’ dotata al suo interno di sei pompanti (cilindretti idraulici) che spingono le pastiglie contro il disco in fase di frenata. E’ in questo momento che si sviluppano temperature che hanno un range operativo dai 350°C ai 1000°C. La pinza, raggiunge invece una temperatura massima di 200°C.
Il disco è caratterizzato lungo la sua superficie radiale, di circa 1500 micro fori che hanno sia la funzione di raffreddamento sia di circolazione dell’aria attraverso la parte centrale del mozzo, e del cerchio ruota. Dietro al disco, si può notare la vera e propria presa d’aria di raffreddamento, che suddivide in micro filetti il flusso per il raffreddamento delle varie componenti. Interessante, peraltro, come il lato interno della presa d’aria sia ormai caratterizzato da molteplici pinne, e alette ricurve, che hanno la funzione strategica di ridurre le turbolenze ai lati del diffusore, tra cui il “tyre squirt” cioè le turbolenze generate dalla deformazione del fianco dei pneumatici a pieno carico.
Come funziona l’impianto?
Passando ora alla spiegazione del funzionamento dell’impianto in sé, si affronta forse la parte più complessa di questa analisi. Il pedale, agisce sui due circuiti separati, anteriore e posteriore, messi in pressione tramite i due rispettivi “master cylinders” (pompe), che mettono in pressione il fluido idraulico contenuto nei rispettivi serbatoi. Mentre la pressione del pedale è trasferita in modo tradizionale, direttamente al fluido contenuto nel circuito anteriore per mezzo del rispettivo master cylinder, non è così per quello posteriore. In pratica, la pressione si trasferisce ad una prima porzione di circuito, connesso con la “compliance chambre”, un simulatore di pressione che trasforma la pressione idraulica del fluido in impulso elettrico indirizzato alla MGU-K. La rotazione degli elementi interni di quest’ultima viene rallentata, generando come conseguenza l’effetto frenate che essa produce, trasmesso al circuito posteriore tramite un attuatore elettroidraulico. Questo, infatti, riceve l’impulso in uscita dalla MGU-K, più o meno intenso a seconda che sia nella fase di carica o di rilascio dell’energia, e trasferisce la conseguente coppia frenante al circuito posteriore, in pressione. Quindi la pressione sull’asse posteriore è di fatto generata sia dallo stato di carica sia dalla ripartizione in termini di pressioni iniziali inviate dai rispettivi master cylinders.
Ciò spiega perché a causa del malfunzionamento della MGU-K di Ricciardo a Monaco, il pilota abbia trasferito il 7 percento di coppia frenante all’avantreno. In questo modo, è riuscito a sforzare di meno il motogeneratore cinetico che non caricava ma che si surriscaldava dunque riducendo il suo effetto frenante. In pratica se ci fosse stata una ripartizione con prevalenza al retrotreno si sarebbe estremizzato il problema sino al cedimento totale del motogeneratore.
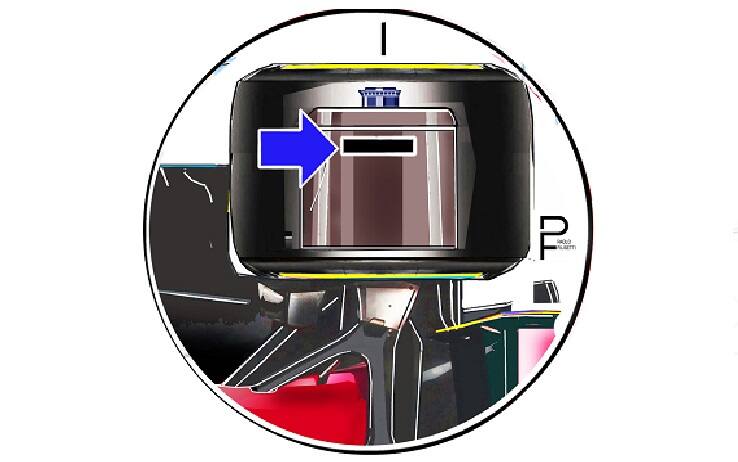